4.2.5三環(huán)減速機(jī)多齒嚙合的研究
三環(huán)減速機(jī)的內(nèi)齒環(huán)板和外齒輪構(gòu)成內(nèi)嚙合齒輪副,是三環(huán)傳動(dòng)的核心所莊。對(duì)于齒數(shù)差較多的內(nèi)齒輪副,其重合度有足夠大的數(shù)值。而對(duì)于齒數(shù)差很小的內(nèi)齒輪副,由于采用了短齒或超短齒以及較大的嚙合角,因此其重合度急劇下降。無論是以傳遞動(dòng)力為主要目的,還是以傳遞運(yùn)動(dòng)為主要目的,為了保待齒輪傳動(dòng)的連續(xù)性,理論上重合度應(yīng)大于1。在少齒差內(nèi)齒輪副中,由于相鄰的若干對(duì)輪齒之間的齒廓間距十分靠近,在運(yùn)轉(zhuǎn)時(shí)因變形而成為多對(duì)齒接觸,提高了少齒差傳動(dòng)的承載能力。
對(duì)于由主動(dòng)輪和從動(dòng)輪組成的齒輪副除滿足彈性力學(xué)的一般方程外,在齒面嚙合點(diǎn)法向上滿足位移非嵌入條件,在切向方向滿足庫侖摩擦定律。只要主動(dòng)輪輸入轉(zhuǎn)矩一定,根據(jù)輪齒嚙合面的接觸狀態(tài),其嚙合面可以分為三種邊界狀態(tài)。對(duì)于由主動(dòng)輪和從動(dòng)輪組成的接觸問題,可將其分成兩個(gè)獨(dú)立的物體,對(duì)主動(dòng)輪和從動(dòng)輪分別建立在整體坐標(biāo)系下的有限元基本方程:
[KI]{UI}={PI}+{RI} (4-14)
[KⅡ]{UⅡ}={PⅡ}+{RⅡ} (4-15)
式中 [KI],[KⅡ]——主動(dòng)輪、從動(dòng)輪的剛度矩陣;
{UI},{UⅡ}——主動(dòng)輪、從動(dòng)輪的節(jié)點(diǎn)位移向量;
{PI},{PⅡ}——作用于主動(dòng)輪、從動(dòng)輪的外載荷向量;
{RI},{RⅡ}——接觸力向量。
用rij和uij分別表示輪齒在第i個(gè)接觸點(diǎn)局問坐標(biāo)系j(j=n,t)方向上的接觸力分量和位移分量,局部坐標(biāo)系如圖4-12所示,上標(biāo)(1)、(2)分別表示主動(dòng)內(nèi)齒輪和從動(dòng)外齒輪,則
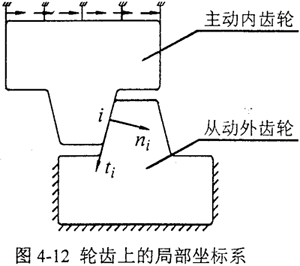
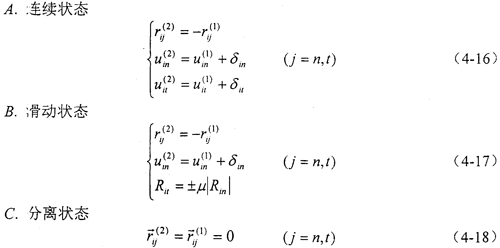
式中 μ——齒面摩擦系數(shù);
δin——齒面接觸點(diǎn)i在法向方向的初始間隙;
δit——齒面接觸點(diǎn)i在切向方向的初始間隙。
由齒面不同接觸狀態(tài)及輪齒接觸問題的總剛度矩陣得到齒輪嚙合面的柔度矩陣方程為:
[fi]{ri(1)}={δi}-{△pi} (4-19)
式中[fi]——嚙合面接觸點(diǎn)的柔度矩陣;
{△pi}——外載荷產(chǎn)生的相對(duì)位移矢量;
在I-DEAS軟件建模模塊中,已經(jīng)給出一個(gè)變量u,它的缺省取值范圍為u∈(0,1),根據(jù)壓力角的實(shí)際取值范圍,可以將其設(shè)為u=tanαi,則輪齒漸開線的參數(shù)方程可以寫成:
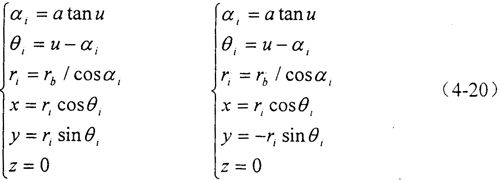
式中 rb——齒輪基圓半徑;
上式參數(shù)方程則給出了兩支以點(diǎn)(rb,0)為基圓上起點(diǎn)的漸開線。實(shí)際上,我們希望得到上述參數(shù)方程所描述的兩支漸開線被齒根圓和齒頂圓所截得一部分。根據(jù)已確定的齒輪參數(shù),經(jīng)過齒根圓和齒頂圓截?cái)啵═rim)、繞分度圓圓心旋轉(zhuǎn)(Rotate)和繞分度圓圓心陣列(Array),然后畫出中心圓,便得到齒輪的平面模型。經(jīng)過拉伸深度為齒輪寬度的拉伸(Extrude),便得到齒輪的動(dòng)態(tài)模型。表4-6所示為齒輪建模過程中的參數(shù)。
表4-6齒輪建模參數(shù)
類別 |
項(xiàng)目 |
分度圓直徑 |
分度圓弧齒厚 |
分度圓齒厚 所對(duì)中心角 |
分度圓上兩支漸開線 所對(duì)中心角 |
漸開線需旋 轉(zhuǎn)角度 |
變位外齒輪 |
147mm |
8.4073652mm |
6.55383° |
1.708561° |
4.13119° |
變位內(nèi)齒輪 |
154mm |
1.913044mm |
1.423498° |
1.708564° |
0.142533° |
根據(jù)內(nèi)、外齒輪嚙合時(shí)的幾何位置分別計(jì)算出各接觸齒對(duì)的初始間隙,各接觸齒對(duì)的初始間隙如表4-7所示。由三環(huán)減速機(jī)傳動(dòng)可知,內(nèi)齒輪為主動(dòng)輪,外齒輪為從動(dòng)輪,因此邊界條件處理為約束內(nèi)齒輪副的徑向方向和約束外齒輪副周邊,載荷轉(zhuǎn)矩施加在內(nèi)齒輪切線方向上。接觸齒對(duì)的有限元模型如圖4-13所示。根據(jù)內(nèi)、外齒輪的結(jié)構(gòu),設(shè)置單元類型、大小及材料特性,輪齒嚙合屬于平面應(yīng)力問題,選取四節(jié)點(diǎn)單元進(jìn)行分析計(jì)算,四節(jié)點(diǎn)單元節(jié)點(diǎn)厚度取為相應(yīng)的內(nèi)、外齒輪厚度。由Meshing模塊共生成四邊形單元10503個(gè),節(jié)點(diǎn)11066個(gè),運(yùn)用I-DEAS軟件,根據(jù)前述的誤差分析,采用間隙單元法,建立約束集和解集,運(yùn)用Model Soltion模塊求得結(jié)果。
表4-7 內(nèi)外輪齒齒廓間的最小間隙 (mm)
齒對(duì)號(hào) |
5-5 |
4-4 |
3-3 |
2-2 |
1-1 |
2′-2′ |
3′-3′ |
4′-4′ |
5′-5′ |
間隙 |
0.042 |
0.021 |
0.015 |
0.008 |
0 |
0.008 |
0.015 |
0.021 |
0.042 |
經(jīng)過間隙單元法迭代計(jì)算,得到嚙合過程中,由于輪齒的變形而形成了多齒接觸。圖4-14所示為由于輪齒的變形,形成了5個(gè)齒的接觸,以及載荷在輪齒之間的分配比例。當(dāng)有5個(gè)齒參與嚙合時(shí),最大主應(yīng)力為73MPa;假定內(nèi)、外齒輪的1號(hào)齒在齒面上b點(diǎn)相互接觸,圖4-15所示為輪齒接觸時(shí),外齒輪上載荷最大的輪齒1號(hào)面的齒面載荷分布情況:圖4-16所示為輪齒接觸時(shí),內(nèi)齒輪上載荷最大的輪齒1號(hào)面的齒面載荷分布情況。
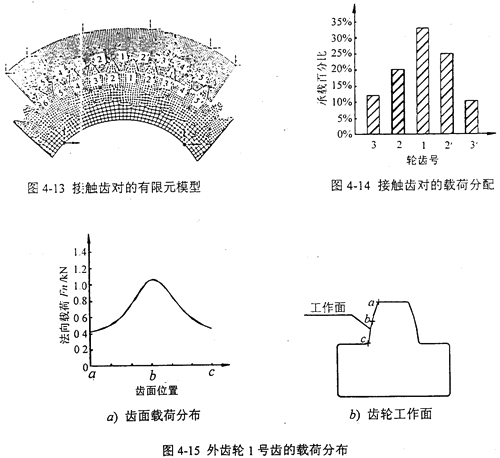
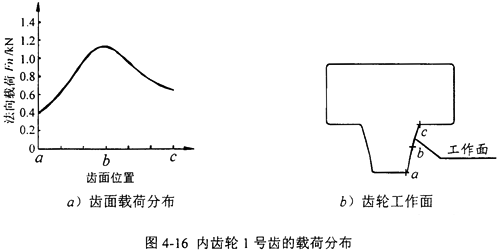
4.2.6三環(huán)減速機(jī)強(qiáng)度的校核
三環(huán)減速機(jī)二級(jí)傳動(dòng)屬于少齒差傳動(dòng),少齒差傳動(dòng)輪齒工作面上的接觸強(qiáng)度不是其在承載能力上的薄弱環(huán)節(jié),尤其是輪齒工作表面上的疲勞點(diǎn)蝕破壞未見發(fā)生過。一般不進(jìn)行其齒面接觸強(qiáng)度校核,而只進(jìn)行其齒根彎曲強(qiáng)度校核。因?yàn)樯冽X差傳動(dòng)的g-b齒輪副為內(nèi)嚙合齒廓的相互接觸,其齒廓曲率中心位于同一方向,而且兩曲率半徑ρ1和ρ2的值較為接近。因此,其輪齒承載后所產(chǎn)生區(qū)接觸應(yīng)力較小。
對(duì)于本文提出的三環(huán)減速機(jī)來說,它的傳動(dòng)參數(shù)如表4-8所示:
表4-8三環(huán)減速機(jī)的傳動(dòng)參數(shù)
一級(jí)傳動(dòng)比i1 |
二級(jí)傳動(dòng)比i2 |
總傳動(dòng)比i=i1·i2 |
輸入轉(zhuǎn)速n |
輸出扭矩T |
35/23 |
21 |
735/23 |
1440r/min |
875N·m |
本文中的三環(huán)減速機(jī)的第二級(jí)傳動(dòng)參數(shù)如表4-9所示:
表4-9 第二級(jí)傳動(dòng)參數(shù)
內(nèi)齒輪齒數(shù)Z2 |
外齒輪齒數(shù)Z1 |
模數(shù)mn |
嚙合角α′ |
齒形角α |
44 |
42 |
3.5mm |
37.356° |
20° |
由于三環(huán)傳動(dòng)同時(shí)嚙合的齒數(shù)多,由前述的分析可知,在傳動(dòng)中共有五個(gè)齒參與嚙合,因此至少可按兩齒均勻受力來校核齒根彎曲強(qiáng)度。因采用30°切線法求齒形系數(shù),故這種計(jì)算方法是極其粗略的,在下面章節(jié)還將進(jìn)行比較精確的有限元分析。
對(duì)于本文的三環(huán)減速機(jī),假定載荷分布均勻,本章只校核一塊兩側(cè)環(huán)板和外齒輪的齒根彎曲強(qiáng)度。每一塊兩側(cè)環(huán)板承受扭矩1/4T,環(huán)板寬度b=19mm,外齒輪承受扭矩T,齒寬b=86mm。則計(jì)算齒根彎曲應(yīng)力為:
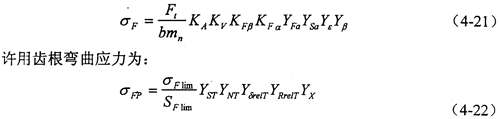
式中 各系數(shù)的意義參見機(jī)械工程手冊(cè)。
根據(jù)本文的三環(huán)減速機(jī)的實(shí)際應(yīng)用情況和結(jié)構(gòu),環(huán)板和外齒輪的材料皆是45號(hào)鋼調(diào)質(zhì)處量,可取σFlim=290N/mm2選取各項(xiàng)系數(shù)代入上式,求得彎曲強(qiáng)度如表4-10所示。
表4-10 環(huán)板和外齒輪的輪齒彎曲強(qiáng)度 (MPa)
外齒輪許用應(yīng)力
σFP1 |
環(huán)板輪齒許用應(yīng)力
σFP2 |
外齒輪計(jì)算應(yīng)力
σF1 |
環(huán)板輪齒計(jì)算應(yīng)力
σF2 |
424.6 |
437.3 |
183.8 |
204 |
取最小安全系數(shù)SFlin=1.5,由計(jì)算結(jié)果可知,σFP≥σF,所以,環(huán)板內(nèi)齒輪、外齒輪均滿足齒根彎曲強(qiáng)度要求。
三環(huán)減速機(jī)的一級(jí)傳動(dòng)是漸開線圓柱齒輪傳動(dòng),第一級(jí)的承載能力取決于接觸強(qiáng)度。三環(huán)減速機(jī)的第一級(jí)傳動(dòng)參數(shù)如表4-11所示。
表4-11 第一級(jí)傳動(dòng)參數(shù)
輸入齒輪齒數(shù)Z3 |
輸入齒輪齒寬b3 |
輸入齒輪齒數(shù)Z4 |
輸出齒輪齒寬b4 |
模數(shù)m |
齒形角α |
46 |
25mm |
70 |
20mm |
2.5mm |
20° |
校核接觸應(yīng)力,計(jì)算接觸應(yīng)力為:
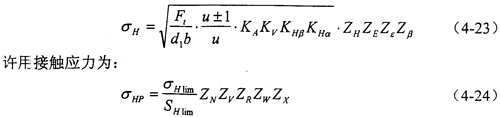
式中各系數(shù)的意義參見機(jī)械工程手冊(cè)。
根據(jù)本文的三環(huán)減速機(jī)的實(shí)際應(yīng)用情況和結(jié)構(gòu),一級(jí)傳動(dòng)齒輪的材料皆是45號(hào)鋼調(diào)質(zhì)處理,可取σHlim=690N/mm2,選取各項(xiàng)系數(shù)代入上式,求得接觸強(qiáng)度如下:
σH=319.74N/mm2
σHP=548N/mm2
取最小安全系數(shù)SHlim=1.5,由計(jì)算結(jié)果可知,σHP≥σH,所以,一級(jí)傳動(dòng)滿足接觸強(qiáng)度要求。
4.2.7三環(huán)減速機(jī)的參數(shù)設(shè)計(jì)
影響三環(huán)減速機(jī)傳動(dòng)綜合性能的參數(shù)很多,其中有傳動(dòng)的中心距2L、一級(jí)定軸傳動(dòng)大、小齒輪參數(shù)(模數(shù)、齒數(shù)、寬度等)、二級(jí)少齒差傳動(dòng)齒輪參數(shù)(模數(shù)、齒數(shù)、寬度、變位系數(shù)、重合度等)、均載機(jī)構(gòu)參數(shù)(均載環(huán)形式、結(jié)構(gòu)等)等。三環(huán)減速機(jī)幾何尺寸及各零部件相對(duì)位置如圖4-17所示。
確定三環(huán)減速機(jī)傳動(dòng)的參數(shù)時(shí),主要考慮了以下幾個(gè)方面:
1.在傳動(dòng)性能指標(biāo)(輸出扭矩、傳動(dòng)比、幾何尺寸等)上,與重慶專用機(jī)械制造公司生產(chǎn)的三齒環(huán)減速機(jī)SCH145一致,這樣可以在同等程度上,比較它們的性能優(yōu)劣;
2.滿足作為行星傳動(dòng)的傳力條件、裝配條件等;
3.一級(jí)定軸傳動(dòng)和二級(jí)少齒差傳動(dòng)盡可能等強(qiáng)度設(shè)計(jì),在保證低速級(jí)一二級(jí)傳動(dòng)強(qiáng)度的基礎(chǔ)上,確定一級(jí)傳動(dòng)的參數(shù);
4.選擇合理的均載環(huán)形式、結(jié)構(gòu),使均載環(huán)具有適宜的剛度、足夠的強(qiáng)度;
5.在滿足給定的傳動(dòng)功率條件下,使三環(huán)減速機(jī)具有較小的體積和重量;
6.合理選擇各個(gè)零部件的結(jié)構(gòu),使加工制造易于實(shí)現(xiàn);
根據(jù)上述原則,對(duì)三環(huán)減速機(jī)進(jìn)行了設(shè)計(jì),其參數(shù)如表4-12所示。
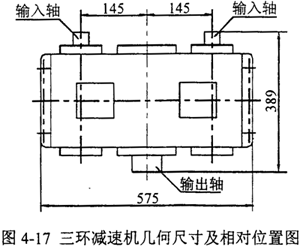
表4-12 三環(huán)減速機(jī)基本參數(shù)表
名稱 |
特性 |
中心距2L |
290mm |
一級(jí)傳動(dòng)小齒輪模數(shù)、齒數(shù)、寬度 |
2.5mm、46、25mm |
一級(jí)傳動(dòng)大齒輪模數(shù)、齒數(shù)、寬度 |
2.5mm、70、20mm |
二級(jí)傳動(dòng)輸出齒輪模數(shù)、齒數(shù)、寬度、變位系數(shù) |
3.5mm、42、86mm、1.142 |
二級(jí)傳動(dòng)兩側(cè)環(huán)板內(nèi)齒輪模數(shù)、齒數(shù)、寬度、變位系數(shù) |
3.5mm、44、19mm、1.407 |
二級(jí)傳動(dòng)中間環(huán)板內(nèi)齒輪模數(shù)、齒數(shù)、寬度、變位系數(shù) |
3.5mm、44、38mm、1.407 |
二級(jí)傳動(dòng)重合度 |
1.05 |
二級(jí)傳動(dòng)嚙合角 |
37.356° |
均載方式 |
金屬彈性環(huán)均載 |
均載環(huán)形式 |
n=4m+4型金屬彈性環(huán) |
4.2.8 三環(huán)減速機(jī)的結(jié)構(gòu)設(shè)計(jì)
根據(jù)三環(huán)減速機(jī)傳動(dòng)的基本參數(shù)以及這種傳動(dòng)的傳遞的功率情況,進(jìn)一步對(duì)三環(huán)減速機(jī)傳動(dòng)進(jìn)行結(jié)構(gòu)設(shè)計(jì)。表4-13所示為三環(huán)減速機(jī)結(jié)構(gòu)參數(shù)。
表4-13 三環(huán)減速機(jī)的結(jié)構(gòu)參數(shù)表
名稱 |
特性 |
偏心套外圓直徑 |
ф45mm |
偏心套偏心距 |
4.18mm |
一級(jí)輸入軸軸承型號(hào) |
左端NU204/P6,右端NU204/P6 |
偏心軸軸承型號(hào) |
左端NU205/P5,右端NU205/P5 |
二級(jí)輸出軸軸承型號(hào) |
左端6211,右端6211 |
環(huán)板軸承型號(hào) |
NU209/P6 |
均載環(huán)結(jié)構(gòu) |
ф2mm,內(nèi)、外圓周各均布八個(gè)凸臺(tái) |
箱體結(jié)構(gòu) |
焊接、部分式 |
密封形式 |
骨架密封圈和O型密封圈密封 |
潤滑方式 |
油池潤滑 |
根據(jù)三環(huán)減速機(jī)的基本參數(shù)和結(jié)構(gòu)參數(shù),設(shè)計(jì)出三環(huán)減速機(jī)的傳動(dòng)工作圖如圖4-18所示。
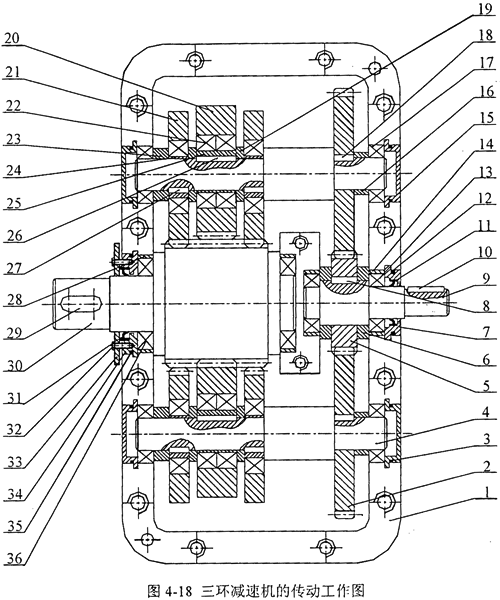
4.2.9三環(huán)減速機(jī)的效率計(jì)算
機(jī)械效率η反映了驅(qū)動(dòng)力所作的功在機(jī)械中的利用程度,它表示為輸出功與輸入功的比值。

式中 Wr——輸出功;
Wd——輸入功;
Wf——損耗功。
本文研究的三環(huán)減速機(jī)是由一級(jí)定軸圓柱齒輪傳動(dòng)和二級(jí)三環(huán)少齒差傳動(dòng)組成,它的效率η由一級(jí)傳動(dòng)效率和二級(jí)傳動(dòng)效率串聯(lián)而成,即
η=η1η2 (4-26)
一級(jí)定軸輪系機(jī)械效率概略計(jì)算取η1=0.98。
二級(jí)少齒差傳動(dòng)的機(jī)械效率η2有理論計(jì)算值和實(shí)測(cè)值兩種,而以實(shí)測(cè)值為評(píng)價(jià)依據(jù)。理論值不可能與實(shí)測(cè)值相同,但在設(shè)計(jì)時(shí)要進(jìn)行理論計(jì)算。
對(duì)于少齒差行星傳動(dòng)的總效率η2,可以認(rèn)為主要由四部分串聯(lián)而成,即
η2=ηeηbηwηM (4-27)
式中 ηe——行星機(jī)構(gòu)的嚙合效率;
ηb——轉(zhuǎn)臂軸承的效率;
ηw——輸出機(jī)構(gòu)的效率;
ηM——液力損失的效率。
由上式可見,少齒差行星傳動(dòng)的總效率是考慮到輪齒嚙合損失、軸承摩擦損失、輸出機(jī)構(gòu)傳動(dòng)損失和液力損失的效率。
三環(huán)減速機(jī)傳動(dòng)是一種新型的三相并列少齒差行星傳動(dòng),沒有輸出機(jī)構(gòu),它的每一相傳動(dòng)效率η2參考少齒差傳動(dòng)計(jì)算如下:
η2=ηeηbηM (4-28)
1.行星機(jī)構(gòu)的嚙合效率ηe
由嚙合功率法可以得到:

式中 ηH——轉(zhuǎn)化機(jī)構(gòu)的嚙合效率。
三環(huán)傳動(dòng)機(jī)構(gòu)的轉(zhuǎn)化機(jī)構(gòu)為定軸少齒差內(nèi)齒輪副,對(duì)于本文研究的三環(huán)減速機(jī),因α′>αa1,節(jié)點(diǎn)p在嚙合線B1B2外,故轉(zhuǎn)化機(jī)構(gòu)的效率計(jì)算如下:

式中fg——嚙合過程中齒面的摩擦系數(shù),一般取fg=0.06~0.10。
對(duì)于本文的三環(huán)減速機(jī),各項(xiàng)數(shù)值代入上式得:ηe=0.968。
2.轉(zhuǎn)臂軸承的效率ηb

式中 TB——摩擦力矩;
TH——轉(zhuǎn)臂轉(zhuǎn)矩。
概略計(jì)算時(shí)可近似地取ηb=0.98~0.995。
3.液力損失的效率ηM

式中 P——傳遞的功率,kw;
vH——圓周速度,m/s;
b——浸入油中的齒輪的寬度,mm;
E°——在工作溫度下油的恩氏粘度,條件度;
Z∑——嚙合齒輪副齒數(shù)和。
選取上述參數(shù),計(jì)算得ηM=0.95。
綜上所述,兩級(jí)三環(huán)減速機(jī)的總效率:
η=η1η2 =η1ηeηbηM=0.98×0.968×0.99×0.95==89.2%
4.2.10三環(huán)減速機(jī)的裝配條件
三環(huán)減速機(jī)與其它行星傳動(dòng)裝置一樣,存在一個(gè)裝配條件的問題。裝配條件指的是將三個(gè)內(nèi)齒環(huán)板均布地裝配在兩根高速輸入軸上,并使這三個(gè)內(nèi)齒環(huán)板與輸出外齒輪嚙合時(shí),保證嚙合的瞬時(shí)相位差為180°。
下面來分析它的裝配條件,由于本文提出的新型三環(huán)減速機(jī)環(huán)板相互之間的相位差為180°,所以在分析時(shí),可以只分析兩塊環(huán)板的裝配情況。圖4-19所示為裝配條件分析圖,在兩塊環(huán)板的偏心所構(gòu)成的π角內(nèi),外齒輪1的齒數(shù)為:
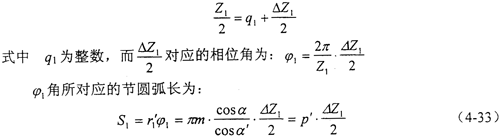
式中P′為節(jié)圓齒距。
在兩片內(nèi)齒環(huán)板的偏心所構(gòu)成的π角內(nèi),環(huán)板上的內(nèi)齒輪2的齒數(shù)為:
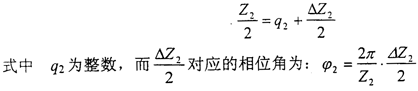
φ2角所對(duì)應(yīng)的節(jié)圓弧長為:

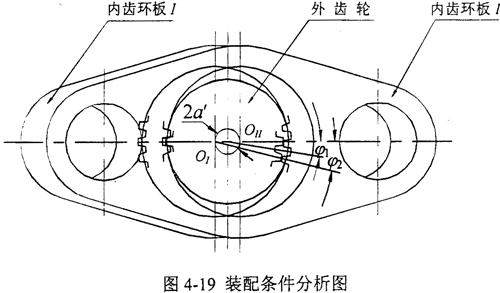
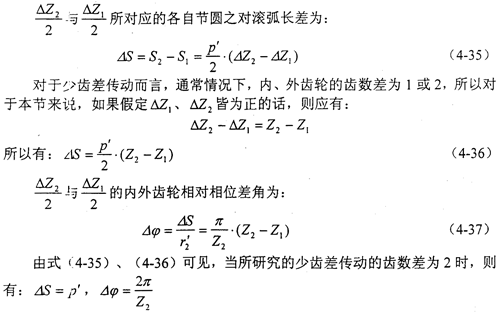
也就是說:當(dāng)一個(gè)內(nèi)齒環(huán)板與外齒輪在某一位置嚙合時(shí),另一塊環(huán)板與外齒輪各自節(jié)圓之對(duì)滾弧長差為節(jié)圓齒距,相對(duì)相位差角為內(nèi)齒輪一個(gè)齒所對(duì)應(yīng)的圓心角,此時(shí)另一塊環(huán)板在該位置剛好能夠裝入。換句話說,對(duì)于本文的三環(huán)減速機(jī),按照4.3的制造工藝,就可以將三片內(nèi)齒環(huán)板均布地安裝在兩根高速偏心輸入軸上,并且保證它們之間的瞬時(shí)相位差呈180°角。
在裝配時(shí),將中間環(huán)板繞其軸線旋轉(zhuǎn)180°并且翻轉(zhuǎn),一則保證它們之間的相位差為180°,二則補(bǔ)償由于加工而引起的偏心誤差,進(jìn)一步提高均載性能。
4.3本章小結(jié)
本章在三環(huán)減速機(jī)力學(xué)分析和均載機(jī)構(gòu)研究的基礎(chǔ)上,對(duì)三環(huán)減速機(jī)的設(shè)計(jì)、制造和裝配的若干問題進(jìn)行了深入的探討和研究
變位系數(shù)的確定是少齒差內(nèi)嚙合傳動(dòng)設(shè)計(jì)的關(guān)鍵。本章在分析少齒差內(nèi)嚙合的兩個(gè)主要限制條件的基礎(chǔ)上,推導(dǎo)了用插齒刀加工的少齒差內(nèi)嚙合變位系數(shù)的牛頓迭代公式,不僅滿足給定的重合度和齒廓不重迭干涉系數(shù)的要求,而且保證標(biāo)準(zhǔn)頂隙,迭代得到的嚙合角較小。
內(nèi)齒環(huán)板和偏心套是三環(huán)減速機(jī)的關(guān)鍵傳動(dòng)零部件,本章應(yīng)用I-DEAS軟件對(duì)內(nèi)齒環(huán)板和偏心套進(jìn)行有限元分析,用來指導(dǎo)結(jié)構(gòu)設(shè)計(jì)。
對(duì)三環(huán)減速機(jī)的少齒差內(nèi)嚙合多齒嚙合問題進(jìn)行了定量分析,得到嚙合齒對(duì)間載荷分布規(guī)律,對(duì)三環(huán)減速機(jī)的強(qiáng)度校核具有指導(dǎo)意義。
兩級(jí)三環(huán)減速機(jī)第一級(jí)傳動(dòng)的承載能力取決于接觸強(qiáng)度,第二級(jí)傳動(dòng)的承載能力取決于齒根彎曲強(qiáng)度。因此對(duì)第一級(jí)漸開線圓柱齒輪傳動(dòng)進(jìn)行接觸強(qiáng)度校核,對(duì)第二級(jí)少齒差傳動(dòng)進(jìn)行齒根彎曲強(qiáng)度校核。
內(nèi)齒環(huán)板是三環(huán)減速機(jī)傳動(dòng)的關(guān)鍵,本章深入討論內(nèi)齒環(huán)板的加工制造。
本章對(duì)提出的相位差為180°的三環(huán)減速機(jī)的裝配條件作了分析和研究。
上一頁
下一頁